The house rebuilding project is going well. We’ve finished all the framing, and the higher ceilings and more open floorplan are hinting at a level of awesomeness that surprises even me. A picture from just this morning:
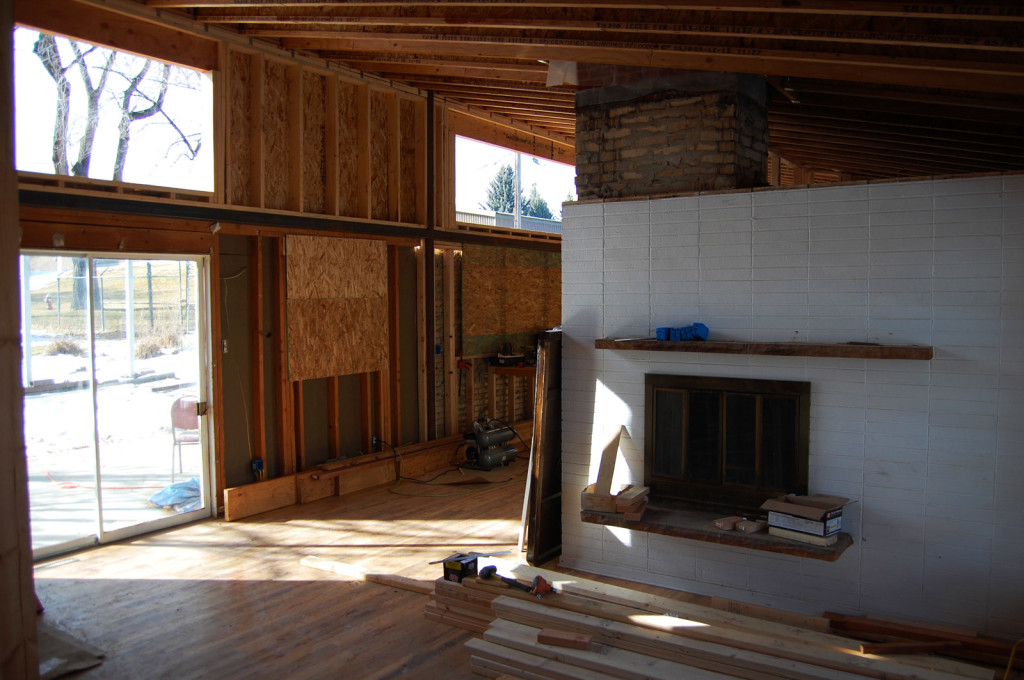
Here is the new living room and the kitchen around the corner in the back. Old ceiling height was at the bottom of that steel beam. 2 more giant window openings still to come behind those plywood squares.
While I’ve destroyed and rebuilt quite a few houses for other people, this is the first one I have been fortunate enough to create from nearly scratch for my own family, so I am treating it as a bit of a science experiment. I want to build neat energy-saving features into it, but they need to be cost-effective and homegrown whenever possible.
Any old rich guy can hire the top architect and boutique builder to make him the latest LEED-Platinum superhouse to show off in Dwell magazine… at $1000 per square foot. But with energy cheap and skilled labor and high-end home materials expensive, it takes more thought and experimentation to save energy AND money at the same time. And one of these experimental projects is to build my own radiant under-floor heating system.
If you have never heard about this, you’ll want to tune in. The dominant heating method in the US right now is the forced air furnace – a big box in your basement that blows air (and dust) through a huge network of bulky air tubes so it can reach all parts of your house through floor vents. It works, but it is not elegant: they make noise, waste a surprising amount of interior space with ducts and chases, and are a hassle to install or upgrade.
When my small construction company was building some houses from the ground up a few years ago, the architect highly recommended that we use hydronic (radiant) heat instead of forced air. “It is a world of difference”, he said, “To have that silent warmth radiating at you through the floor instead of just blowing around some hot air.”
Unfortunately, when I got quotes from some plumbers for this type of heating system, the cost was astronomical: $35,000 or more, when a full conventional heating system was only $10,000 installed. Since these homes were being built to sell, on a tight budget to compete with other houses in the forced-air price range, I reluctantly decided to skip the luxury option. Plus, the passive solar design in our architecture would ensure that the furnace was used only lightly anyway.
Now, the picture has changed. I have learned to do my own plumbing, and new technologies have come down in price that make radiant heat much more affordable. After quite a few long nights of research and online training videos, I have bought all the necessary parts and we are about to put this sucker in.
What is Hydronic Radiant Heating?
Have you ever walked past a large brick building long after the sun goes down, and felt warmth all over your body even without touching the wall? How about feeling the heat from a hot bed of campfire coals even when sitting some distance away? This is radiant heat in action: a warm surface shines out infrared light (also known as heat), which directly warms your skin. With a hot campfire on a still mountain night, you can feel completely warm even when the air temperature around you is below freezing.
This same concept applies nicely to warming a house with hydronic radiant heat: warm water circulates in tubes under your floor, causing the floor to warm up and shine heat at you from all directions. There are no ducts and no blowing dust, and the system operates silently. And because the system is warming your skin directly at the same time it warms the air of your house, you feel warmer at a lower temperature setting, which allows you to keep the house cooler, saving energy. But the best part may be that you have constantly warm feet, wherever you go in your house.
So how do we build one of these systems? In a nutshell, you need something to heat the water (sometimes called a boiler), a network of tubing under your floor, and a pump to circulate that water through all that tubing:
While the concept is simple, my summary leaves out a lot of detail. When you look at the typical “boiler room” in a luxury house, there are all sorts of valves and sensors, and miles of meticulously soldered copper from the $35,000 plumber. I mean, shit, does this look like an easy do-it-yourself project to you?
On top of that, hydronic heating is an art and science unto itself, with things like ΔT, GPM, BTU/hr, and R-value calculations involved. If you can get through all that, you’re faced with boilers that start at $2000, a complicated selection of parts that nobody except the experts really understands (you won’t be getting advice at Home Depot on building one of these systems), and all sorts of other hurdles.
However, after digging through all this rubble, I found a few simplifications that bring the cost and complexity of radiant heat way down, to make it a DIY-compatible project for the average handy Mustachian. The tricks I’m applying for my system:
- Using drinking-water-safe components allows an “open loop” system which requires fewer valves and allows item 2:
- Using a single tankless water heater for both hot water and house heating cuts out the $2000-$4000 boiler cost. I chose this extremely efficient Rheem Tankless unit that runs only about $1200.
- A single variable speed circulator pump eliminates most of the loss and loop size calculations by sensing the water temperature and adjusting its speed automatically (this also saves energy).
- Using a pre-made manifold from Rifeng allows easy multi-zone control and adjustment, without the need to ever mess with the tubing after you install it.
- And of course, everything is done in PEX, to eliminate the cost, slow installation, and boiler-room heat loss of copper pipes.
Boiling it all down, the system I ended up with is relatively simple, and I drew it out for you in this picture:
So far, this is a work in progress. I have already run this by a system designer and received his nod of approval, and completed some of the installation, so I am sure we can get this to work. But there are surely improvements to be made.
The great thing about this blog is that there are many people reading right now (including professional plumbers) who have already done this, so if you have any suggestions on how to improve or simplify it further, it would be much appreciated and I will update the article as new information is received. I will also publish a second post when everything is done, to show a few of the steps in progress and the finished pictures.
Reader corrections so far:
- Add the expansion tank before the pump, not after it as currently shown
- Watch out for Legionella bacteria growth in an open-loop system like this. While rare, the bacteria is dangerous. Exactly the same risk exists if you have a tank-type water heater and keep the water under about 120F. Solution: make sure my tankless unit is hot (legionella dies above 122F, so perhaps 130 or higher), to exterminate bacteria. Also, drain or flush the heating loops during the offseason so the water does not sit stagnant for months.
- OR, create two-loop system with a heat exchanger in between the two loops, so the heating water never touches the hot tap water. This requires oxygen-barrier PEX and an air eliminator. You can also buy tankless heaters with two independent loops: one for heating, one for potable water.
- Add a check valve on the 3/4″ return line so cold water cannot sneak back into the manifold instead of going to the Rheem (I guess this could happen when the pump is off)
- Actually, add a check valve on every loop, just to make sure there are no flow surprises and water goes the direction you want it to. Otherwise, cold water can be drawn through loops unexpectedly.
- Many tankless heaters (including the Rheem I recommend above) are not warrantied for use in heating systems. This is fine for me, as I find warranties are generally useless anyway. But it is good to note.
- Further criticism about this experiment showed up here on the forum of the useful site called heatinghelp.com. While the thread almost convinced me that I am an idiot, the thing is that a similar discussion forms somewhere on the internet about every single article that ever appears on this blog. Many plumbers spend their days cursing this site just because I recommend doing some of your own plumbing with PEX, for example. The problem is that my fellow tradesmen tend to use anecdotes rather than statistics to make these safety decisions. The experiment will go on undeterred, but I will make a point of doing some tests with my friend who works at the city’s drinking water treatment/analysis lab.
What About Cooling?
Every house should be designed to suit its own climate. Here in Colorado, we have intense sun nearly every day but much cooler nights due to our elevation 5000 feet above sea level. So the house has loads of South-facing windows to capture heat and more loads of thermal mass to smooth out day and night temperature swings.
In the summer, this picture flips around: the Earth tilts so the sun is nearly overhead (and the large overhangs I built onto the house shade the windows from the rest of it). You keep the windows closed during the 90F days and the interior stays cool. On summer nights, the temperatures drop below 60F, so you run a large fan blowing out the day’s heat to cool everything down and begin the cycle anew.
I find this strategy (along with not being a Giant A/C Wussy) allows us to live happily without turning on our A/C in Colorado. But there’s always a backup: most modern houses without ducts use a ductless mini-split air conditioning system for cooling. These can be more efficient than central A/C systems, because you only cool the rooms where heat is building up. I will add a system like this if necessary, but we will be sure to test out a summer without air conditioning first, since the place is likely to be even more comfortable than our current house, even without cooling.
As the final cheat sheet, here is my shopping cart from PexSupply, my preferred supplier of plumbing stuff. There are a few extra things in my shopping cart for building out the bathrooms, but in general this is a complete system for a 1500 square foot house: about $1100, with free shipping and no sales tax. Add in the water heater and you have a complete heat and hot water system that costs less than a single low-efficiency furnace.
An efficiency upgrade to this system: I also purchased two boxes of aluminum heat reflector plates from Amazon which should improve heat transfer and efficiency slightly. Cost was $2.45 per 4-foot plate ($245 for each box of 100).
Update: After building the system with these, I feel it was highly worthwhile as it makes installation faster and cleaner, and improving heat transfer is a worthwhile goal with wood floors – while they work well, you do need all the heat you can get.
Update: One Year Later
This system is now up and running and you can read the results in the update article here:
The Radiant Heat Experiment – Did it Work?
Leave a Reply
To keep things non-promotional, please use a real name or nickname
(not Blogger @ My Blog Name)
The most useful comments are those written with the goal of learning from or helping out other readers – after reading the whole article and all the earlier comments. Complaints and insults generally won’t make the cut here, but by all means write them on your own blog!